PFMEA va DFMEA oʻrtasidagi asosiy farq shundaki, PFMEA biznes boʻlimining muayyan jarayonidagi mumkin boʻlgan nosozliklarni tahlil qilishga yordam beradi, DFMEA esa mahsulot dizaynidagi mumkin boʻlgan nosozliklarni tahlil qilishga yordam beradi.
FMEA (Failure Mode Effects Analysis) usuli operatsion boshqaruvdagi jarayonning potentsial nosozlik usullarini va tizimdagi mahsulotni ishlab chiqish bosqichida dizaynni aniqlashga yordam beradi va nosozliklar ehtimoli va jiddiyligi asosida nosozliklarni tasniflaydi. Muvaffaqiyatsizlik rejimi mijozga ta'sir qiladigan dizayn, jarayon yoki elementdagi har qanday nuqson yoki xatolarni anglatadi. "Ta'sir tahlili" muvaffaqiyatsizliklarning oqibatlarini o'rganishni anglatadi.
PFMEA nima?
PFMEA "Process Failure Mode Effects Analysis" ning qisqartmasi. Ushbu metodologiya operatsiyalar darajasidagi jarayonlarda potentsial nosozlik usullarini aniqlashi mumkin. Umuman olganda, PFMEAni texnik jihatdan tajribali jamoa olib boradi. Asosiy jarayon xatolik rejimining taʼsirini toʻgʻirlash yoki minimallashtirish uchun ishlamay qolish sabablari boʻyicha tegishli maʼlumotlarni yigʻishdir.
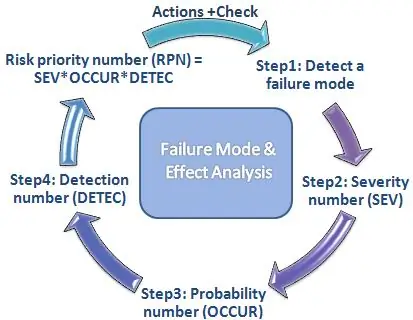
Bundan tashqari, PFMEA barcha turdagi tashkilotlar tomonidan qoʻllaniladigan tuzilgan vositadir. Bu nosozlik usullarining ta'sirini yaratishga yordam beradi va xavfni bartaraf etish uchun zarur bo'lgan harakatlarni birinchi o'ringa qo'yadi. PFMEA potentsial xavflarni kamaytirish uchun har qanday yangi jarayonlarni boshlashdan oldin hujjatlashtiriladi va taqdim etiladi. Bundan tashqari, tizimni doimiy takomillashtirishga erishish uchun buni amaldagi jarayonlarga qo'llash ham mumkin.
DFMEA nima?
DFMEA qisqartmasi "Design Failure Mode Effects Analysis" ning qisqartmasi. Ushbu metodologiya ishlab chiqish bosqichida mahsulot dizaynidagi mumkin bo'lgan nosozliklarni aniqlashga yordam beradi. Ko'pgina hollarda muhandislar buni real vaziyatda yoki foydalanishda dizayndagi nosozlik ehtimolini o'rganish uchun protsedura sifatida ishlatadilar.
DFMEA uchun asosiy vosita muhandislari DFMEA matritsasi hisoblanadi. Ushbu matritsa texnik xususiyatlar, chiqarilgan sanalar, qayta ko'rib chiqish sanalari va jamoa a'zolari bilan bog'liq ma'lumotlarni to'plash va hujjatlashtirish uchun tuzilmani taqdim etadi. Umuman olganda, DFMEA - bu texnik tajribaning jamoaviy ishi va ehtimol o'zaro faoliyat guruhdir. Bundan tashqari, DFMEA dizayndagi mumkin bo'lgan nosozliklarni bartaraf etishda jarayonni boshqarish vositalariga tayanmaydi
PFMEA va DFMEA oʻrtasidagi oʻxshashliklar qanday?
- PFMEA va DFMEA - bu muvaffaqiyatsizlik rejimi effektlari tahlilining ikki turi.
- DFMEA va PFMEAdagi asosiy qadamlar oʻxshash, ammo ularda ikkita turli ilova mavjud.
- DFMEA ham, PFMEA ham mumkin boʻlgan nosozliklar, xavflarning jiddiyligi, mavjud nazorat, tavsiyalar va tavsiya etilgan harakatlardan keyin yaxshilanishlarni bildiradi.
- Ikkalasining ham yakuniy maqsadi mahsulotlar va ishlab chiqarishdagi katta nuqsonlarni kamaytirish yoki oldini olishdir.
- Bu metodologiyalar dizayn yoki ekspluatatsiya xarajatlarini ham kamaytirishi mumkin.
- Bundan tashqari, DFMEA da ba'zi nosozliklarni yumshatib bo'lmaydi. Ushbu nosozliklar PFMEA ga o‘tkazilishi va mahsulotni yaxshilash uchun kerakli nazoratni olishi mumkin.
PFMEA va DFMEA oʻrtasidagi farq nima?
PFMEA va DFMEA o'rtasidagi asosiy farq shundaki, PFMEA jarayonlarni o'z ichiga oladi, DFMEA esa mahsulot dizaynini o'z ichiga oladi. DFMEA ning asosiy maqsadi mahsulot dizaynidagi potentsial nosozliklarni aniqlash, PFMEA ning asosiy maqsadi esa jarayonlarning mumkin bo'lgan nosozliklarini aniqlashdir. DFMEA ning asosiy ko'rib chiqilishi mahsulot sxemasidan foydalangan holda amalga oshiriladi, PFMEA esa texnologik oqim diagrammasi yordamida amalga oshiriladi. PFMEA va DFMEA o'rtasidagi yana bir farq shundaki, PFMEA operatsion darajada, DFMEA esa ishlab chiqish bosqichida sodir bo'ladi.
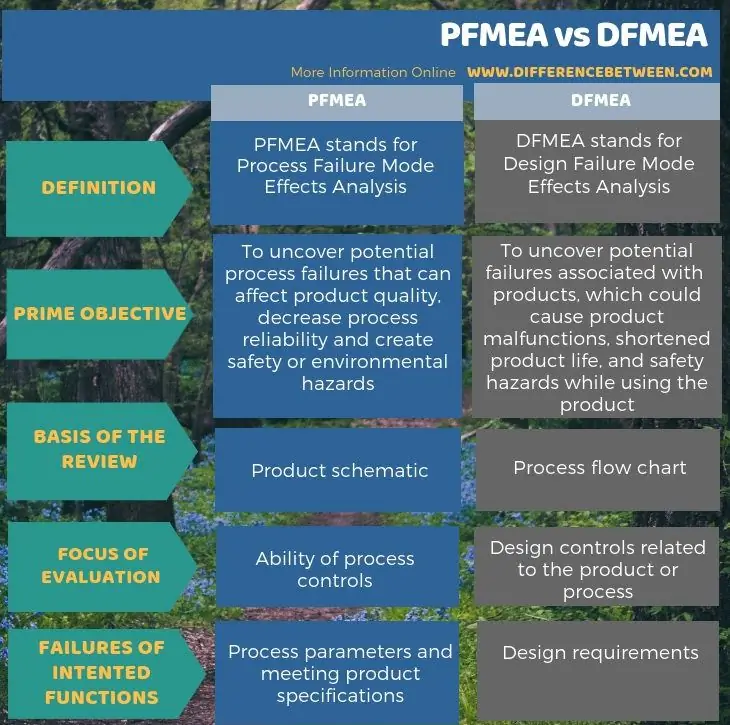
Xulosa- PFMEA va DFMEA
PFMEA va DFMEA o'rtasidagi asosiy farq shundaki, PFMEA operatsion darajasida ma'lum bir jarayonning mumkin bo'lgan nosozliklarini tahlil qilishga yordam beradi, DFMEA esa dizayn va ishlab chiqish darajasida mahsulot dizaynidagi mumkin bo'lgan nosozliklarni tahlil qilishga yordam beradi. Bundan tashqari, bu metodologiyalar ishlab chiqarish xarajatlarini kamaytiradi va mahsulotlarni ishga tushirishda yuzaga kelishi mumkin bo'lgan nosozliklarni ham kamaytiradi.