Sinterlash va tavlanish oʻrtasidagi asosiy farq shundaki, sinterlash muayyan materiallardan ichki stressni olib tashlash uchun issiqlikni qoʻllash jarayonidir, tavlanish esa aglomerat metall zarrachalariga issiqlikni qoʻllash jarayonidir.
Sinterlash va tavlanish issiqlik bilan ishlov berishni o'z ichiga olgan muhim sanoat jarayonlaridir. Bu jarayonlar turli ish bosqichlari va turli ish sharoitlarini ham o‘z ichiga oladi.
Sinterlash nima?
Sinterlash - bu metallning erish nuqtasi ostidagi issiqlikni qo'llash orqali metallning kichik zarralarini bir-biriga payvandlash jarayoni. Bu ma'lum materiallardan ichki stresslarni olib tashlash uchun issiqlikni qo'llashni o'z ichiga oladi. Bu jarayon asosan po'lat ishlab chiqarishda foydalidir. Sinterlash jarayonidan foydalanish murakkab shakllarni shakllantirish, qotishmalar ishlab chiqarish va yuqori erish nuqtalariga ega bo'lgan metallar bilan oson ishlash qobiliyatini o'z ichiga oladi.
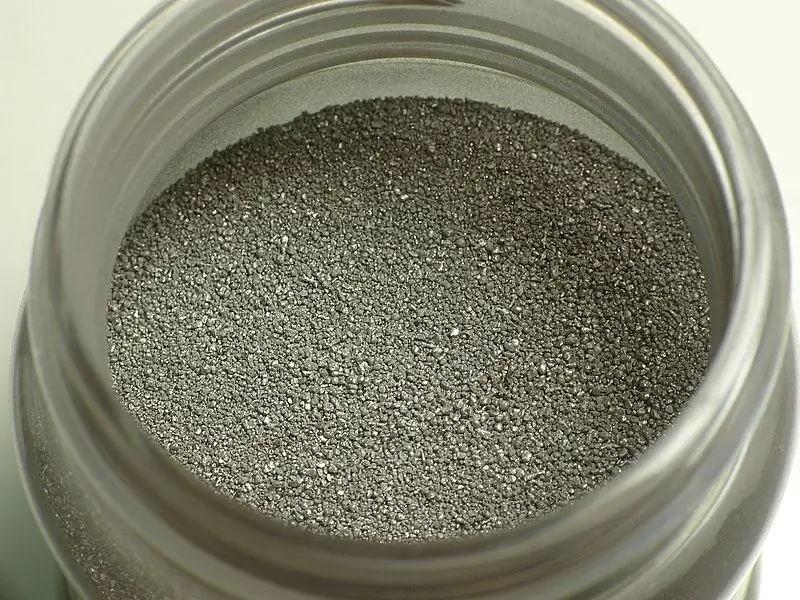
01-rasm: Temir kukuni
Ishlab chiqarish jarayonida biz temir rudasidan kukunli temir to'shagini ishlatishimiz kerak. Ushbu temirni ishlatishdan oldin uni koks bilan aralashtirish kerak. Keyin temir to'shagi gaz gorelkasi yordamida yoqiladi. Keyin kuygan qism harakatlanuvchi panjara bo'ylab o'tkaziladi. Bu erda yonish reaktsiyasini boshlash uchun panjara orqali havo olishimiz kerak. Keyin juda yuqori issiqlik hosil bo'ladi, bu esa metallning mayda zarralarini bo'laklarga olib keladi. Ushbu bo'laklar po'lat hosil qilish uchun yuqori o'choqda yoqish uchun mos keladi. Bundan tashqari, sinterlash jarayoni keramika va shisha ishlab chiqarishda ham muhimdir.
Tavlanish nima?
Tavlanish - bu issiqlik bilan ishlov berish jarayoni bo'lib, unda biz metallni ustun haroratgacha qizdirib, biroz vaqt ushlab turishimiz va egiluvchanlikni yaxshilash uchun uni sovutishimiz kerak. Yuvish - kerakli kimyoviy va fizik xususiyatlarni olish uchun materialni yumshatish jarayoni. Ushbu kerakli xususiyatlardan ba'zilari ishlov berish, payvandlash, o'lchov barqarorligi va boshqalarni o'z ichiga oladi.
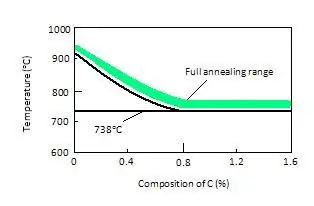
02-rasm: tavlanish harorati diapazonlari
Tavlanish jarayoni metallni kritik haroratgacha yoki unga yaqin qizdirishni o'z ichiga oladi (kritik harorat - bu metallning kristal fazasi o'zgargan harorat). Bunday yuqori haroratga qizdirish uni ishlab chiqarishga yaroqli qiladi. Issiqlikdan so'ng, pech yordamida metallni xona haroratiga sovutishimiz kerak.
Metalning sekin sovishi tozalangan mikro tuzilmani hosil qiladi. Bu tarkibiy qismlarni qisman yoki to'liq ajratishi mumkin. Yuvish bilan ishlov berish jarayoni sof metallar va qotishmalarga ham tegishli. Ushbu jarayonga ko'ra, qora metallarning ikkita turi mavjud:
- Toʻliq tavlangan temir qotishmalari (juda sekin sovutish jarayonidan foydalaning)
- Tavlangan temir qotishmalarini qayta ishlash (sovutish tezligi tezroq bo'lishi mumkin)
Guruch, kumush va mis kabi boshqa metallar toʻliq tavlanishi mumkin, lekin ularni suvda oʻchirish usuli yordamida tez sovutish kerak.
Sinterlash va tavlanish o'rtasidagi farq nima?
Sinterlash va tavlanish issiqlik bilan ishlov berishni o'z ichiga olgan muhim sanoat jarayonlaridir. Sinterlash va tavlanish o'rtasidagi asosiy farq shundaki, sinterlash ma'lum materiallardan ichki stresslarni olib tashlash uchun issiqlikni qo'llashdir, tavlanish esa aglomeratsiya metall zarralariga issiqlikni qo'llashdir.
Sinterlash - bu metallning erish nuqtasi ostidagi issiqlikni qo'llash orqali metallning kichik zarralarini bir-biriga payvandlash jarayoni. Yuvish - bu issiqlik bilan ishlov berish jarayoni bo'lib, biz metallni ustun haroratgacha qizdirib, uni biroz vaqt ushlab turishimiz va egiluvchanligini yaxshilash uchun sovutishimiz kerak.
Quyida sinterlash va tavlanish oʻrtasidagi farq jadvali keltirilgan.
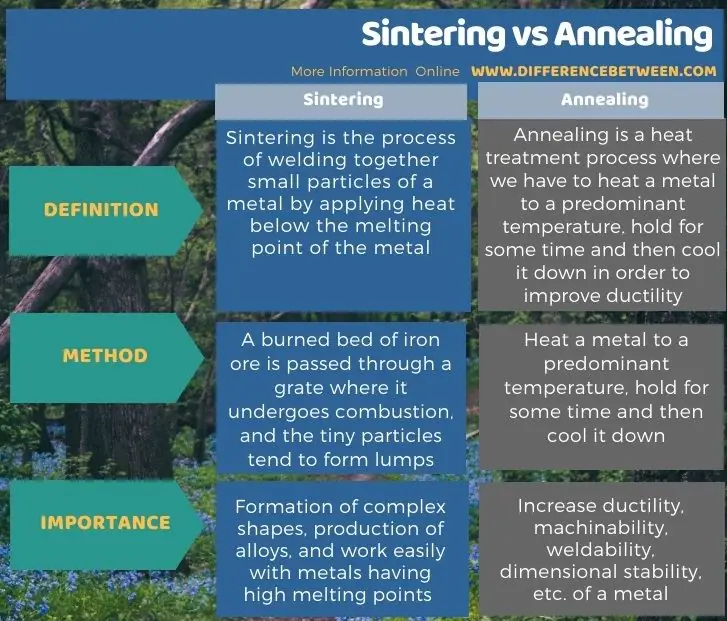
Xulosa - Sinterlash va tavlanish
Sinterlash va tavlanish issiqlik bilan ishlov berishni o'z ichiga olgan muhim sanoat jarayonlaridir. Sinterlash va tavlanish o'rtasidagi asosiy farq shundaki, sinterlash ma'lum materiallardan ichki kuchlanishlarni olib tashlash uchun issiqlikni qo'llashdir, tavlanish esa metall zarralarini aglomeratsiya qilish uchun issiqlikni qo'llashdir.